Utilization of Cassava Pulp from Starch Production Process and from Biogas System to Produce Value-Created Micro- and Nano-Cellulose
Keywords:
Cassava Pulp, Chemical Treatment, Nanocellulose, Starch Waste, Sustainable MaterialAbstract
Background and Objective: Cassava pulp (CP) is a solid waste byproduct from the starch extraction process in the cassava industry, presenting significant environmental challenges such as foul odor and water contamination. In Thailand, the cassava industry has adopted the circularity concept to practice resource minimization, waste reduction, and value creation. Strategies have been developed to utilize CP for energy generation and low-value applications such as animal feed. Additionally, CP can be converted into biogas through anaerobic digestion. Another promising approach is the production of high-value products such as micro- and nano-cellulose. Micro-cellulose consists of micro-sized fibers isolated from plants, and can serve as a reinforcing material in the textile and pulp industries. Nano-cellulose, on the other hand, exhibits such properties as biodegradability and high surface area. These properties make micro-cellulose and nano-cellulose ideal for use as reinforcing polymers, food packaging, and pharmaceuticals. The present study aimed to produce micro- and nano-cellulose from cassava pulp obtained from (i) a starch production process and (ii) a biogas system (CP and CPbiogas, respectively) using acid hydrolysis.
Methodology: The study focused on the extraction of micro-cellulose and nano-cellulose from CP and CPbiogas. Starch was removed from cassava pulp using enzymatic treatment (α-amylase). Lignocellulosic fiber was then isolated using 0.7% (w/v) NaClO2 and alkaline with 17.5% (w/v) NaOH to obtain micro-cellulose. Subsequently, the micro-cellulose was hydrolyzed with H2SO4 to produce nano-cellulose. The two-factor Central Composite Design (CCD) was utilized to optimize the design of the experiment. The two factors were H2SO4 concentration, ranging from 46-74% w/w and reaction time ranging from 48-132 min. In total, 11 experimental conditions were scheduled. The micro-cellulose and nano-cellulose obtained were characterized to determine their crystallinity indices using X-ray diffraction, their particle size using dynamic light scattering, and their morphology using scanning electron microscopy.
Main results: The study revealed that after the removal of starch by α-amylase, 87.5% of the starch was extracted from CP, while CPbiogas had all its starch removed. Following bleaching and alkaline treatment, a fibrous fraction with cellulose contents of 91% and 88% (CP and CPbiogas respectively) was obtained. The micro-cellulose extracted from CP and CPbiogas had average particle sizes of 104.9 µm and 106 µm and crystallinity indices of 68% and 70%, respectively. The optimal hydrolysis conditions for nano-cellulose extraction from CP and CPbiogas were 60% H2SO4 and 132-min reaction time. Nano-cellulose particles smaller than 100 nm comprised 10% and 12% of the total nano-cellulose yields from CP and CPbiogas, respectively, with an increase in crystallinity index to 71% and 76%. Statistical analysis reveals that increasing the reaction time could result in a higher yield of nano-cellulose.
Conclusions: Micro-cellulose and nano-cellulose derived from CP and CPbiogas in exhibit promising characteristics, including crystallinity indices of 71% and 76% for nano-cellulose obtained from CP and CPbiogas, respectively. Such characteristics demonstrate significant potential for innovative industrial applications in the paper, composite, and textile industries. In comparison, commercial nano-cellulose typically has a crystallinity index exceeding 80%; the nano-cellulose obtained in this study demonstrates crystallinity indices slightly below commercial standards. Utilizing solid wastes such as CP (CP and CPbiogas) to produce micro-cellulose and nano-cellulose addresses waste management challenges, while creating economic value from a previously underutilized byproduct.
Practical Application: The presented approach aligns with the principles of circular economy, where waste materials are repurposed into valuable resources, enhancing resource efficiency and sustainability. The study highlights the significant potential of converting CP waste into high-value cellulose products, contributing to the advancement of sustainable industrial practices and the development of innovative materials.
References
Lerdlattaporn, R., Phalakornkule, C., Trakulvichean, S. and Songkasiri, W., 2021, “Implementing Circular Economy Concept by Converting Cassava Pulp and Wastewater to Biogas for Sustainable Production in Starch Industry,” Sustainable Environment Research, 31 (1), pp. 1-12.
Sowcharoensuk, C., 2023, Industry Outlook 2023-2025: Cassava Industry [Online], Available: https://www.krungsri.com/en/research/industry/industry-outlook/agriculture/cassava/io/cassava-2023-2025#:~:text=Demand%20for%20cassava%20will%20continue,of%20fresh%20cassava%20in%202023. [15 April 2023]
Trakulvichean, S., Chaiprasert, P., Otmakhova, J. and Songkasiri, W., 2019, “Integrated Economic and Environmental Assessment of Biogas and Bioethanol Production from Cassava Cellulosic Waste,” Waste and Biomass Valorization, 10 (3), pp. 691-700.
Scarlat, N., Fahl, F., Dallemand, J.F., Monforti, F. and Motola, V., 2018, “A Spatial Analysis of Biogas Potential from Manure in Europe,” Renewable and Sustainable Energy Reviews, 94, pp. 915-930.
Aziz, T., Farid, A., Haq, F., Kiran, M., Ullah, A., Zhang, K. and Al Jaouni, S.K., 2022, “A Review on the Modification of Cellulose and its Applications,” Polymers, 14 (15), 34 p.
Reshamwala, S., Shawky, B.T. and Dale, B.E., 1995, “Ethanol Production from Enzymatic Hydrolysates of AFEX-treated Coastal Bermudagrass and Switchgrass,” Applied Biochemistry and Biotechnology, 51, pp. 43-55.
Omran, A.A.B., Mohammed, A.A., Sapuan, S.M., Ilyas, R.A., Asyraf, M.R.M., Rahimian Koloor, S.S. and Petrů, M., 2021, “Micro-and Nanocellulose in Polymer Composite Materials: A Review,” Polymers, 13 (2), p. 231.
Chen, X., Deng, X., Shen, W. and Jiang, L., 2012, "Controlled Enzymolysis Preparation of Nanocrystalline Cellulose from Pretreated Cotton Fibers," BioResources, 7 (3), pp. 4237-4248.
Chen, X.Q., Pang, G.X., Shen, W.H., Tong, X. and Jia, M.Y., 2019, “Preparation and Characterization of the Ribbon-like Cellulose Nanocrystals by the Cellulase Enzymolysis of Cotton Pulp Fibers,” Carbohydrate Polymers, 207, pp. 713-719.
Zhang, Y., Lu, X.B., Gao, C., Lv, W.J. and Yao, J.M., 2012, “Preparation and Characterization of Nano Crystalline Cellulose from Bamboo Fibers by Controlled Cellulase Hydrolysis,” Journal of Fiber Bioengineering and Informatics, 5 (3), pp. 263-271.
Spagnuolo, L., Beneventi, D., Dufresne, A. and Operamolla, A., 2024, “High Yield Synthesis of Cellulose Nanocrystals From Avicel by Mechano-Enzymatic Approach,” ChemistrySelect, 9 (30), pp 1-7.
Wang, H., Xie, H., Du, H., Wang, X., Liu, W., Duan, Y., Zhang, X., Sun, L., Zhang, X. and Si, C., 2020, “Highly Efficient Preparation of Functional and Thermostable Cellulose Nanocrystals Via H2SO4 Intensified Acetic Acid Hydrolysis,” Carbohydrate Polymers, 239, 10 p.
Travalini, A.P., Prestes, E., Pinheiro, L.A. and Demiate, I.M., 2018, “Extraction and Characterization of Nanocrystalline Cellulose from Cassava Bagasse,” Journal of Polymers and the Environment, 26, pp. 789-797.
Thiex, N.J., Manson, H., Anderson, S., Persson, J.Å. and Collaborators: Anderson, S., Bogren, E., Bolek, G., Budde, D., Ellis, C., Eriksson, S., Field, G., Frankenius, E., Henderson, C., Henry, C., Kapphahn, M., Lundberg, L., Manson, H., Moller, J., Russell, M., Sefert-Schwind, J. and Spann, M., 2002, “Determination of Crude Protein in Animal Feed, Forage, Grain, and Oilseeds by Using Block Digestion with a Copper Catalyst and Steam Distillation Into Boric Acid: Collaborative Study,” Journal of AOAC International, 85 (2), pp. 309-317.
Doehlert, D.C. and Duke, S.H., 1983, “Specific Determination of α-Amylase Activity in Crude Plant Extracts Containing β-Amylase,” Plant Physiology, 71 (2), pp. 229-234.
Van Soest, P.V., Robertson, J.B. and Lewis, B.A., 1991, “Methods for Dietary Fiber, Neutral Detergent Fiber, and Nonstarch Polysaccharides in Relation to Animal Nutrition,” Journal of Dairy Science, 74 (10), pp. 3583-3597.
Mandal, A. and Chakrabarty, D., 2011, “Isolation of Nanocellulose from Waste Sugarcane Bagasse (SCB) and Its Characterization,” Carbohydrate Polymers, 86 (3), pp. 1291-1299.
Chen, Y., Liu, C., Chang, P.R., Cao, X. and Anderson, D.P., 2009, “Bionanocomposites Based on Pea Starch and Cellulose Nanowhiskers Hydrolyzed from Pea Hull Fibre: Effect of Hydrolysis Time,” Carbohydrate Polymers, 76 (4), pp. 607-615.
Hu, H., Liang, W., Zhang, Y., Wu, S., Yang, Q., Wang, Y., Zhang, M. and Liu, Q., 2018, “Multipurpose Use of a Corncob Biomass for the Production of Polysaccharides and the Fabrication of a Biosorbent,” ACS Sustainable Chemistry & Engineering, 6 (3), pp. 3830-3839.
Abraham, E., Deepa, B., Pothan, L.A., Jacob, M., Thomas, S., Cvelbar, U. and Anandjiwala, R., 2011, “Extraction of Nanocellulose Fibrils from Lignocellulosic Fibres: A Novel Approach,” Carbohydrate Polymers, 86 (4), pp. 1468-1475.
Li, Q., Wei, B., Xue, Y., Wen, Y. and Li, J., 2016, “Improving the Physical Properties of Nano-cellulose Through Chemical Grafting for Potential Use in Enhancing Oil Recovery,” Journal of Bioresources and Bioproducts, 1 (4), pp. 186-191.
Ouyang, X., Wang, W., Yuan, Q., Li, S., Zhang, Q. and Zhao, P., 2015, “Improvement of Lignin Yield and Purity from Corncob in the Presence of Steam Explosion and Liquid Hot Pressured Alcohol,” RSC advances, 5 (76), pp. 61650-61656.
Ghazy, A., Bassuoni, M.T., Maguire, E. and O’Loan, M., 2016, “Properties of Fiber-Reinforced Mortars Incorporating Nano-silica,” Fibers, 4 (1), pp. 1-16.
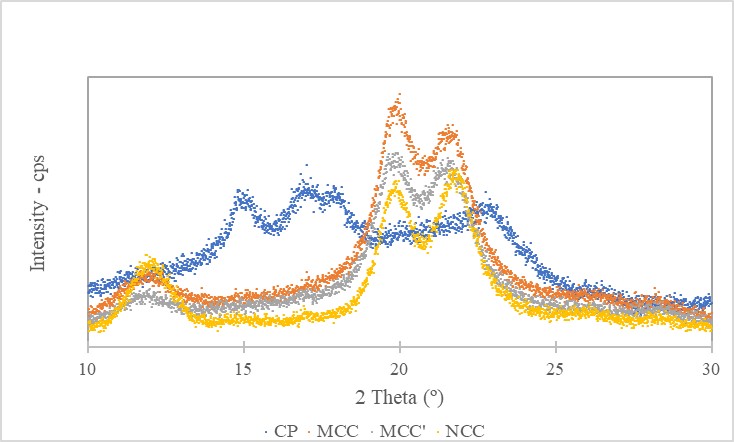
Downloads
Published
How to Cite
Issue
Section
License
Copyright (c) 2024 King Mongkut's University of Technology Thonburi

This work is licensed under a Creative Commons Attribution-NonCommercial-NoDerivatives 4.0 International License.
Any form of contents contained in an article published in Science and Engineering Connect, including text, equations, formula, tables, figures and other forms of illustrations are copyrights of King Mongkut's University of Technology Thonburi. Reproduction of these contents in any format for commercial purpose requires a prior written consent of the Editor of the Journal.